Forni a vuoto
I Vantaggi dei Forni a Vuoto nei Processi ad Alta Temperatura.
Una Rivoluzione Tecnologica
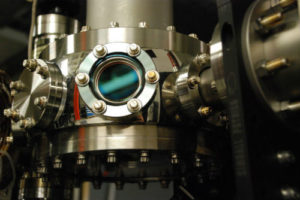
Camera di un forno per vuoto
Nella continua evoluzione dell’industria manifatturiera e dei processi di produzione ad alta temperatura, i forni a vuoto si stanno affermando come una soluzione innovativa che offre una serie di vantaggi significativi. Queste apparecchiature avanzate stanno cambiando il modo in cui le aziende affrontano i processi termici, portando a miglioramenti in termini di efficienza, qualità del prodotto e sostenibilità. In questo articolo, esploreremo i principali vantaggi dei forni a vuoto nei processi ad alta temperatura e come stanno rivoluzionando l’industria.
1. Controllo preciso della temperatura
I forni a vuoto consentono un controllo preciso della temperatura, garantendo che i materiali siano sottoposti a condizioni termiche specifiche. Questo livello di controllo è essenziale in settori quali l’aerospaziale, l’industria automobilistica e l’elettronica, dove le tolleranze strette sono fondamentali per la qualità del prodotto. La temperatura uniforme all’interno del forno a vuoto riduce al minimo la variazione termica, consentendo la produzione di componenti ad alta precisione.
2. Atmosfera controllata
I forni a vuoto possono operare in atmosfere controllate, come vuoto o gas inerte, eliminando il contatto con l’ossigeno e altri gas reattivi. Questo è fondamentale per la lavorazione di materiali sensibili all’ossidazione o alla contaminazione. I processi a vuoto mantengono la purezza del materiale, migliorando la qualità del prodotto finito.
3. Risparmio energetico
Gli impianti di vuoto sono noti per il loro notevole risparmio energetico rispetto ai forni tradizionali. Poiché il riscaldamento avviene all’interno di un ambiente sigillato e isolato, le perdite di calore sono ridotte al minimo. Questo non solo diminuisce i costi operativi, ma contribuisce anche alla riduzione dell’impatto ambientale.
4. Velocità di raffreddamento controllata
I forni a vuoto permettono un raffreddamento controllato, evitando stress termici indesiderati nei materiali. Questa caratteristica è fondamentale per la lavorazione di materiali fragili o componenti critici. La capacità di regolare la velocità di raffreddamento può estendere la vita utile dei materiali e ridurre i tassi di rottura.
5. Flessibilità nei processi
I forni a vuoto sono adatti per una vasta gamma di applicazioni, dall’indurimento e la brasatura al trattamento termico e alla sinterizzazione. La loro flessibilità li rende un investimento ideale per aziende che operano in diversi settori, consentendo loro di ottimizzare i processi di produzione in un unico impianto.
6. Qualità del prodotto superiore
Grazie al controllo accurato della temperatura, all’atmosfera controllata e alla riduzione dello stress termico, i forni a vuoto contribuiscono a migliorare la qualità del prodotto finale. I componenti prodotti in questi forni spesso presentano una maggiore resistenza, una migliore finitura superficiale e prestazioni superiori.
In conclusione, i forni a vuoto rappresentano una rivoluzione nell’industria manifatturiera e nei processi ad alta temperatura. La loro capacità di controllare la temperatura, l’atmosfera e il raffreddamento li rende strumenti indispensabili per la produzione di componenti di alta precisione e materiali di qualità superiore. Inoltre, il risparmio energetico e la versatilità li rendono una scelta ecologica ed economica. Le aziende che adottano questa tecnologia sono in grado di migliorare la loro competitività, offrendo prodotti di qualità superiore e riducendo i costi operativi.
La parte scaldante
La parte scaldante è progettata per distribuire il calore in modo uniforme all’interno del forno a vuoto. Questo è cruciale per evitare variazioni di temperatura significative all’interno della camera di processo, garantendo che i materiali siano riscaldati in modo omogeneo. Questa uniformità è essenziale per la produzione di componenti ad alta precisione e per evitare difetti causati da gradienti termici.
In genere come elemento riscaldante, vengono usate resistenze corazzate o resistenza in grafite. Le nuove tecnologie, tuttavia, tendono a modificare la struttura scaldante sostituendo le resistenze di cui parlavamo, con resistenze infrarossi in quarzo, opportunamente montate su supporti, che garantiscono sia un irraggiamento adeguato, sia una protezione meccanica.
In questo modo, si riescono ad ottimizzare le fasi di riscaldamento, in quanto l’accensione e la temperatura da raggiungere possono essere modulate e controllate in modo perfetto attraverso sistemi di termoregolazione o tramite opportuna interfaccia ad un PLC.
Unica nota da segnalare, è il fatto che il sistema di potenza, controllato esclusivamente da unità statiche dedicate sia ben bilanciato al fine di evitare rotture e fermi macchina.
- Posted by Giuliano
- On Settembre 22, 2016
- 0 Comment